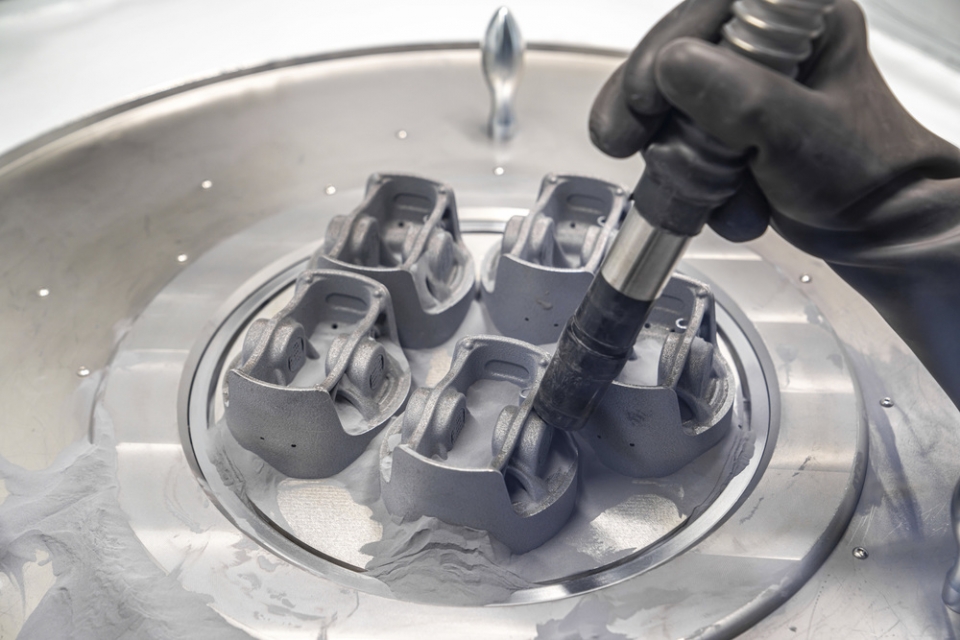
3D 프린팅으로 제작된 피스톤이 고성능 브랜드 포르쉐 라인 슈퍼카에 적용된다. 3D 프린팅으로 제작된 자동차 부품은 강성은 유지하면서 무게가 가벼운 특징을 갖고 있다. 포르쉐는 최근 911 GT2 RS의 고성능 엔진에 적용되는 고강도 피스톤을 3D 프린팅 기술로 제작한다고 밝혔다.
또 말레(Mahle) 및 트럼프(Trumpf)와 고강도 부품 제작에 적층 제조 공정을 사용하는 혁신을 통해, 프로토타입 구조물부터 클래식 스포츠카 부품에 이르기까지 다양한 분야에서 3D 프린팅 기술을 적용할 계획이라고 밝혔다. 3D 프린팅은 피스톤에 작용하는 부하를 최적화된 구조로 제작할 수 있으며 단조 방식으로 생산된 피스톤에 비해 10% 이상 가볍다.
또 기존 방식으로는 제작할 수 없던 피스톤 크라운에 통합된 쿨링 덕트도 가능해진다. 포르쉐 관계자는 "무게를 줄인 3D 프린팅 피스톤으로 엔진 속도는 증가하고 온도 부하가 낮아지며 연소는 최적화한다며 이를 통해 최고출력이 30마력 증가한 730마력에 이를 것"이라고 밝혔다.
3D 프린팅 기술은 별도의 성형 및 주형 툴을 제작할 필요 없이, 구성 부품을 층층이 쌓아 올려 만드는 제작 원리를 기반으로 한다. 어떤 기하학적 형태도 구현 가능하며, 컴퓨터에서 직접 설계 데이터를 공급 받을 수도 있다. 911 GT2 RS의 피스톤은 레이저 금속 용융(LMF) 공정을 통해 고순도 금속 분말로 제조된다. 레이저 빔은 구성 부품 윤곽에 따라 분말 표면에 열을 가하고 녹이게 된다.
한편 포르쉐는 이미 다양한 분야에 적층 제조 공정을 적용해, 3D 프린팅 기술을 활용하고 있다. 지난 5월부터 3D 프린팅 바디 폼 풀 버킷 시트를 911과 718 파생 모델에 이용하고 있으며, 시트 중앙 부분인 시트 및 등받이 쿠션을 부분적으로 3D 프린터로 생산하고 있다.
특히 포르쉐 클래식은 이전에는 구현할 수 없었던 플라스틱, 강철 및 합금 부품을 재생산하고 있다. 포르쉐 959 클러치 릴리즈 레버가 3D 프린터로 제작되고 있으며 약 20종의 재생산 부품이 적층 제조 공정으로 만들어지고 있다.